Originally posted on The Frontier Hub – Industrial Innovation.
Digital transformation is rapidly changing industries into technological havens filled with human and machine interactions. The trend has already brought a wide variety of benefits to the organizations that have plunged into the digital unknown, helping enhance efficiency and productivity through the optimization of daily processes. However, while digital transformation itself is a monumental movement, the application of computing and real-time communications combined in industrial settings driving Industry 4.0 is profoundly changing the world we live in for the better.
Industry 4.0, while having roots that go back two decades, is revolutionizing the way companies manufacture, improve, and distribute their products. Through the integration of innovative technologies, including the Internet of Things (IoT), cloud computing and analytics, AI, and deep machine learning into their production facilities and throughout their operations, organizations are unlocking new possibilities and profits.
“With the combination of more powerful and affordable devices, bigger and better networks, more pervasive access through cellular, WiFi, mesh, and innovation at the edge. The potential of Industry 4.0 is unlimited,” said Jeffrey C. Li, Senior Director, Risk, Governance, Partners, and Projects at ConnX, a digital communications transformation as a service platform provider that integrates SD-WAN, UC collaboration, mobility, security, Artificial Intelligence (AI) and Automation enterprises. “Our customers in the industrial space are instrumenting their factories to improve safety, yield, and profitability, doing so with a mix that connects not only machines but humans and machines.”
The growth of Industry 4.0 has been rapid and staggering, to say the least, as just a couple of years ago, in 2019, the Industry 4.0 market was at USD 70 billion. However, thanks to the recent explosion in adoption, the market is now expected to grow at a CAGR of 17 percent, putting the industry 4.0 market at USD 210 billion by 2026. Currently, the fastest growing sector for Industry 4.0 has been from the industrial sector, primarily within manufacturing organizations.
“Historically, manufacturing has always been on the slower side when it comes to adopting technology, but the potential of Industry 4.0 has changed that notion,” Li explained. “The success of factory automation by pioneering companies is driving every industrial and manufacturing company to invest and re-invest in robotics and Robotic Process Automation (RPA). Digitized shop floors that continuously collect and share data through connected machines, devices, and production systems are growing around the world, and with networking and cloud, large industrial enterprises are now aware of productivity gains, especially in distributed footprints. Now, these companies can support hundreds of locations remotely, lowering costs for field service and extending the life of their equipment while also improving their understanding of where improvements can be made.”
The technology has already been extremely beneficial to factory enterprises, providing insights and helping to manage inventory more efficiently. For example, by using the technology on equipment to acquire and process real-time data, intelligent manufacturing is giving manufacturers a more complete, 360-degree high-fidelity virtual data-driven integrated view of all operations, from suppliers and supply chains.
“While the trend of industry 4.0 is most notably associated with manufacturing currently, the ability to connect humans and data via intelligent technologies transcends any industry barrier,” Li said. “The advantages that industry 4.0 brings to organizations doesn’t stop the factory floor but can play a pivotal role in the improvement of a variety of businesses, regardless of size or vertical.”
Li pointed out one of the areas where industrial innovation is driving massive cost savings: connected field service.
“Companies like ServiceNow have completely transformed how manufacturers connect, control, and optimize expensive equipment and robotics on production lines,” Li said. “Field service describes situations in which authorized technicians perform essential tasks at specific locations. Often, these technicians visit customer-owned properties to install, repair, maintain, or remove systems or equipment, and the associated truck rolls are expensive and often inefficient. This is where human and machine communications and collaboration is making a huge difference.”
Vital field equipment often demands expert installation from trained technicians to make sure that the equipment is set up correctly and is functioning properly. Installation may also include onboarding, answering questions, and training customers on how to properly interact with the equipment.
“To ensure the longest-possible operational life of all offsite equipment, technicians perform maintenance tasks and audits while in the field,” Li said. “This can include corrective maintenance, or equipment repair, or preventative maintenance, or routine inspections, with the third traditional category – proactive maintenance, which are scheduled regularly. Where we are seeing the most growth and potential is in predictive maintenance, which is where the intersection of human and machine communications is most exciting. When a machine can collect and send data into a software platform that analyzes that data in real-time, then alerts the right person or group, problems can be avoided with zero downtime.”
Li said popular collaboration applications, for example, Microsoft Teams, can be leveraged beyond typical virtual meetings and be used to immediately organize the right experts to assist in resolving problems in real-time when machines signal risk.
“Many businesses employ hundreds of field technicians to handle growing demand, especially when it comes to expensive and complex equipment which keep manufacturing lines going in the appliance, automotive, consumer electronics, and other industries,” Li said. “The challenge is to remain competitive with responsive service while also controlling costs. When more can be automated, fewer technicians are needed, and when those technicians are able to connect in real time with a product expert using a collaboration platform, they can provide faster and successful remediation on the first visit.”
Li also noted that with experienced technicians retiring and a limited workforce to replace them, finding better ways to monitor, maintain and fix machinery is imperative. “When assets are owned by the customer, field service organizations struggle to have enough information to provide effective maintenance, which can lead to unplanned downtime,” Li explained. “When assets are leased to the customer, the owners of the equipment are obliged to make sure those assets are as productive and reliable as possible. By using field service management software, including ticketing, work order management, scheduling, customer and asset information, and more, and using collaboration software to keep the process flowing, dispatchers can easily track task progress and technician locations in ways that were never possible before.”
With applications across any manufacturing category, Li says, “the combination of people, experience, knowledge management systems, easy-to-use collaboration tools that can bring in an expert using text messaging, voice sessions, and live video and screen sharing is what will define modern industrial operations and lead to happier customers, and greater profitability.”
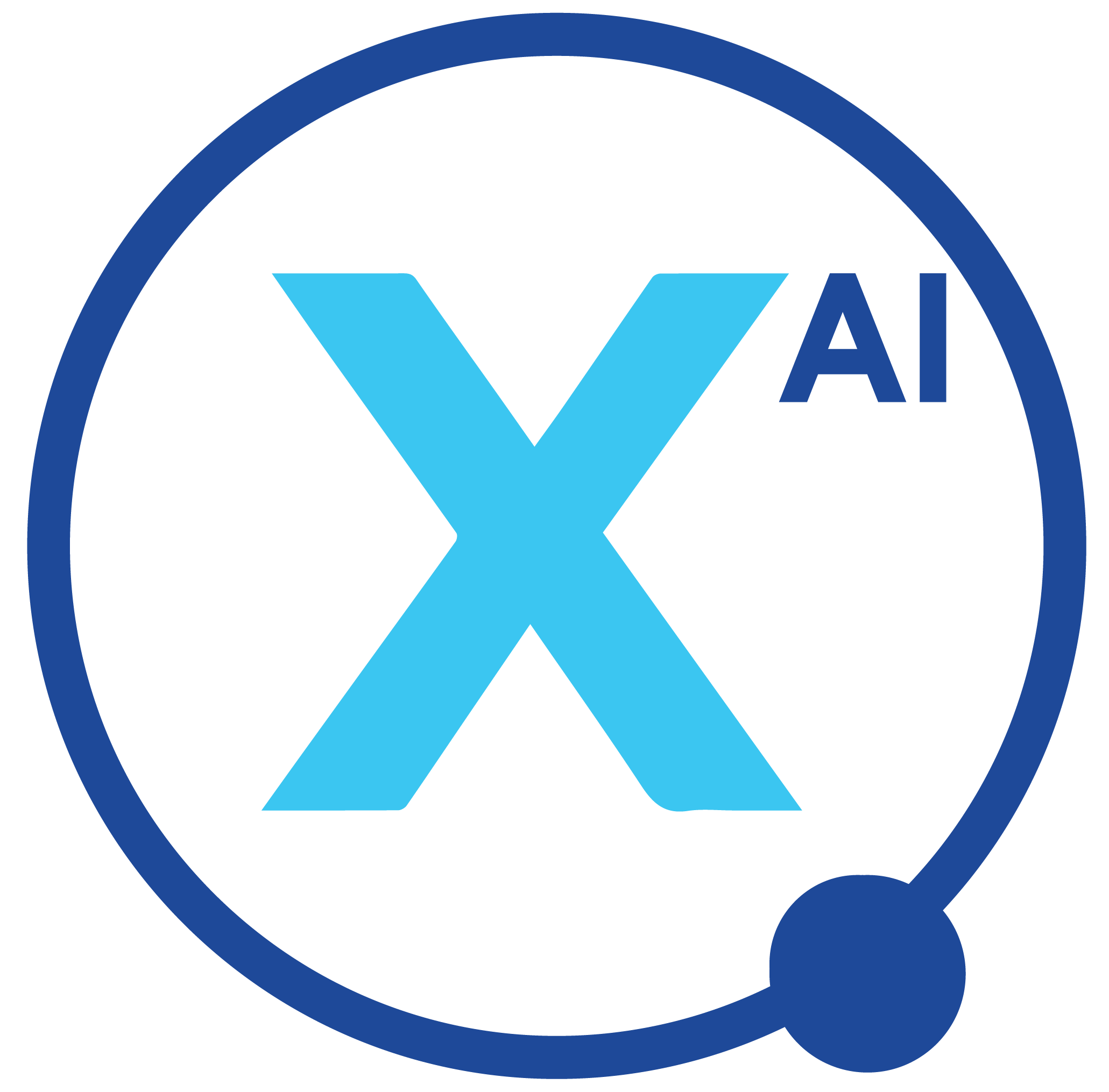
connx marketing