Original post on Industrial Innovation (The Frontier Hub)
As the era of Industry 4.0 continues to evolve and smart factories become more common, manufacturers with a vision are reinventing how products are made in factories where autonomous systems are replacing manually operated and maintained processes.
Decades before IoT and Industrial IoT came on the scene, human smarts made all decisions, with skilled operators relying on years of experience with specific pieces of equipment. Technicians were in place to monitor these machines with visual inspections, scheduled maintenance, and more. Many factories still rely on this approach and produce exceptional products. Still, in an increasingly complex manufacturing world supporting a competitive environment and difficult economy, it’s no longer viable to not “instrument” plants.
“Today, computational capabilities are affordable and ubiquitous, giving even the smallest industrial firms access to data, AI, machine learning, and edge computing, which was previously only used by large players,” said Jeff Li, Senior Director of Strategy, Risk, Governance, Projects, and Partners at ConnX, a managed service provider based near Princeton, New Jersey, serving hundreds of large global enterprises by simplifying business connectivity, collaboration, security, and service assurance. “We are seeing huge demand for more intelligence at the edge of the networks we run for our industrial and manufacturing customers, as they are recognizing how they can use data to improve efficiency, sustainability, quality, and customer experience.”
An intelligent factory is a manufacturing facility that uses advanced technologies such as artificial intelligence and digital twins along with the Internet of Things (IoT), edge networking and computing, and gateways to the cloud to improve efficiency and productivity.
In a smart factory, machines, and other equipment are connected to each other and to a central network, allowing them to communicate and share data in real-time. This enables the factory to respond quickly to changing conditions and customer demands. Smart factories also incorporate automation and robotics to perform tasks more accurately and efficiently than humans.
“The phenomenon we’re seeing is the emergence of Co-Bots,” Li said. “When connected factory platforms are designed to enable productivity, the people working in those factories have much better jobs, with much better tools to work with. We are experiencing growth in collaboration solutions that blend information generated by sensors with human conversations, which is part of the reason why our Microsoft Teams business has grown so fast. Connected Field Service is one of the fastest growing examples of Co-Bots when Teams can bring together the right people in real-time to solve a problem that was predicted by a sensor in a piece of expensive equipment.”
Li said it makes sense that with more sophisticated consumers seeking more sophisticated products – whether EVs, smart home appliances, smartphones, or AR/VR fitness equipment, the complexity associated with modern manufacturing is increasing.
“Moore’s law in the semiconductor industry is a perfect example,” Li said. “In other industries, even if the product isn’t becoming more technologically advanced, technology that improves processes and productivity that leads to greater profits is driving demand for AI at the edge in the factory.”
Li also pointed out that in the Environmental Social and Governance (ESG) world, pressure is mounting when it comes to environmental concerns in production. “Sustainability mandates are forcing suppliers further down the value chain to participate in meeting their customers’ sustainability goals, and every manufacturer we work with is paying attention and investing in this area. Data generated and analyzed at the local and national and even global levels is extremely valuable and only possible with AI and automation.”
One of the challenges that manufacturers face as they begin to collect equipment monitoring data is what to do with it. High-frequency data such as vibration or temperature readings can quickly generate massive quantities of real-time information. Without the tools and strategies in place to parse it, it’s useless and may even become a hindrance.
“As a provider of managed services in the IT and telecom realms,” Li said, “we have developed our orchestration and optimization platform for enterprise networking with intelligence built in. We are able to convey to our industrial and manufacturing customers that data collection is just one part – for example, a sensor on an expensive piece of scientific equipment can indicate when the temperature is rising, but without AI and smart analytics, the factory operators have no actionable data. The breakthrough in communications networking has been to go beyond data and actionable data to autonomous actions – for example, pausing a machine where the temperature indicates the onset of what could be a catastrophic failure.”
Actionable data includes predictive analytics and can be part of a holistic remote field service solution using collaboration software. “No more expensive and slow truck rolls,” Li said. “How does that sound? Our customers are saving millions by monitoring equipment in a predictive rather than reactive way and working with companies like ServiceNow, who today are outfitting their ‘technicians-as-a-service’ with AR and VR glasses for onsite inspections, which connect the tech with the product expert. This is just another example of Co-Bots and collaboration in industrial digitally transformed environments.”
Li closed by predicting massive innovation as edge computing and networking, wireless broadband, and enterprise 5G connectivity continues to grow.
Polaris Market Research last year published a study forecasting that the Smart Factory Market Size & Share Valuation will grow over USD 191.02 Billion by 2030, a CAGR rise of 10.46 percent CAGR.
Polaris defines the Smart Factory as “an advanced factory that uses advanced technologies such as artificial intelligence (AI), machine learning, and connected devices to collect data and share it in real-time continuously. The company can then use the data to handle issues, enhance production processes, and fulfill new demands. Smart factories are part of Industry 4.0, or the fourth industrial revolution, which is driven by digital transformation and automation.”
Polaris also listed cloud connectivity, big data, the Industrial Internet of Things (IIoT), virtual reality (VR) and augmented reality (AR), and others. “These factories provide benefits such as faster problem resolution, better safety & quality control, on-time delivery, and seamless data exchange,” the authors wrote. “The smart factory market size is driven by factors including an increasing focus on energy efficiency, resource optimization, and cost reduction in production operations.”
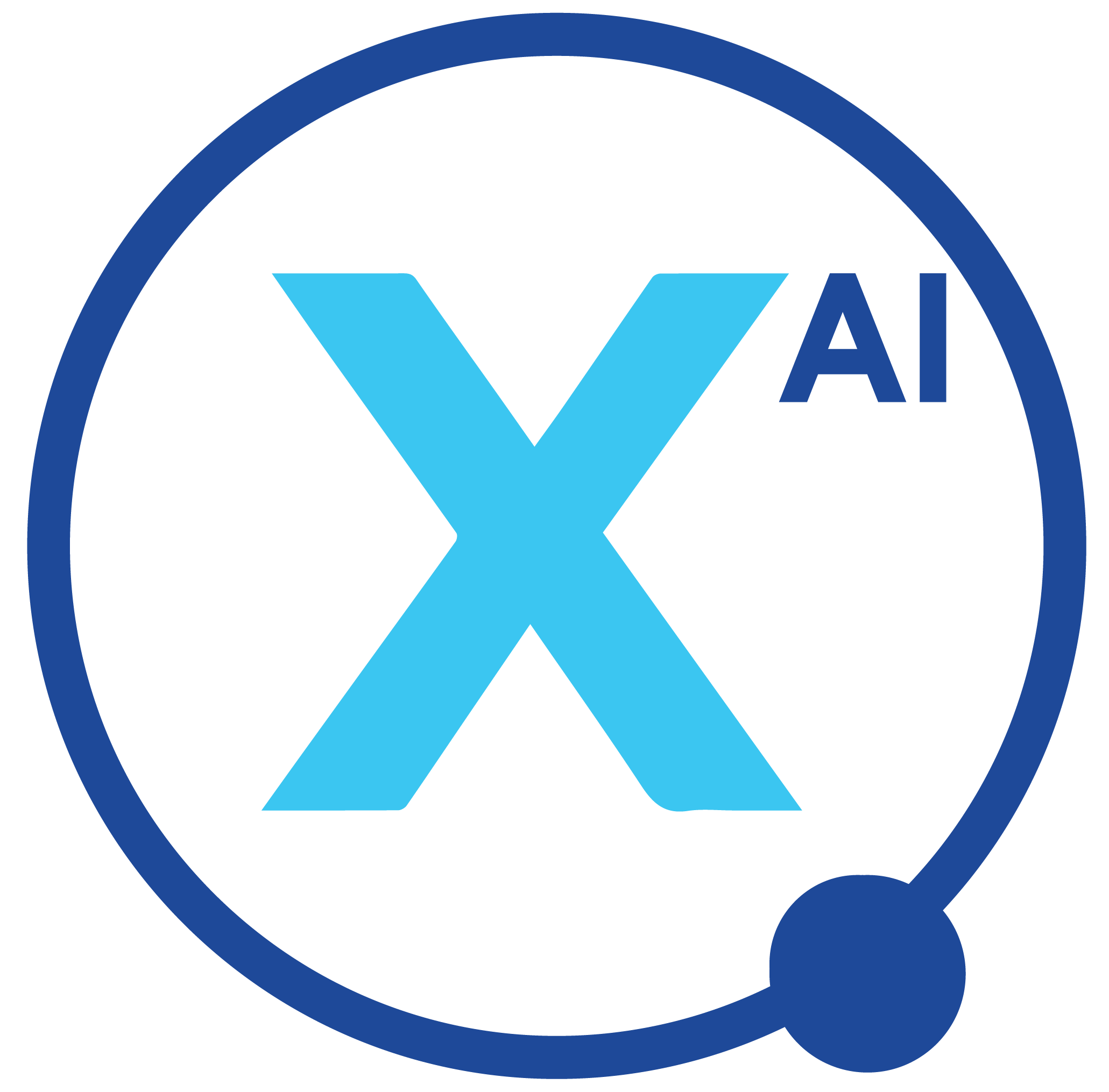
connx marketing